
This may not work very well as there isn’t much of the heater plate in contact with the jar base. I used a 80 degree 12V PTC heater plate again from Amazon fastened to a plastic plate that was then fitted on top of the existing ceramic insulator. With that problem taken care of all I needed to do was replace the switch and the element. Blue and brown wires are not at 240V potential. The refurbished watch cleaning machine showing the underside. To adjust speed I used a XL4016 based voltage regulator from Amazon to adjust the voltage between 2 and 11.5V and this was fastened to the front panel using a block of wood. When it was tested there was a very small amount of wobble and vibration but after adjustment it was reduced to an acceptable level. The motor was then fastened to the original plate so that any mounting brackets would be unnecessary.

Some of the brush housings had to be grinded away with a dremel too. The replacement motor was small enough to fit inside the old motor casing once it had been gutted of the burnt out stator and windings. The old and dangerous parts + wiring removed for disposal This was then fixed in place with two grub screws 180 degrees apart so any small amounts of wobble could be adjusted. Next problem was that the impeller bore was not metric with it being some size between 6 and 7mm so a 6mm metal rod was used to fasten it to the coupling and sellotape to pack out the protruding end to the same size as the bore. This was done on a lathe to ensure it was exactly straight to avoid wobble. The motor shaft was a non standard 3.4mm diameter so I had to purchase a 3mm to 6mm coupling and then bore out the 3mm hole to 3.4mm. The motor was sourced from a HP officejet 6500A which previously served as the carriage motor and despite it’s small size was quite powerful. Now this really is just scrap at this point as it couldn’t be any more broken but cost of a new machine was too prohibitive so I decided to replace it all with low voltage parts. It was questionable what I would be able to do with it given the lack of parts, tools and a decent work area as this had to be done on the kitchen worktop. In short every component on it was faulty with nothing salvageable or repairable at all. I tested all the parts individually and found that the motor had burnt out with it visibly heavily water damaged and rusted, the power switch was open circuit even in both positions, the rheostat was visibly corroded and the heating element was busted.


However upon further inspection I deemed it too unsafe to even plug in so I didn’t bother testing it with power applied.
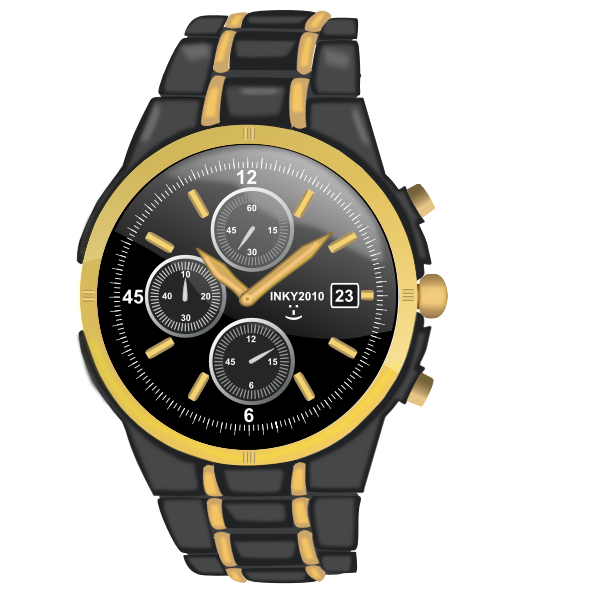
I decided that in order to make this thing somewhat safer it would need to be re-wired and some sort of plate fastened over the base to cover the exposed live parts.
#Armwatch spare machine full
Also the heating element, directly connected to the mains had a jar sat on top of it full of water which is splashed about with an impeller. Simply picking it up whilst plugged in could have resulted in an electric shock. This was a very dangerous machine even when new they didn’t care much for electrical safety in them days! If you turned it over all the live wiring was accessible as was the rheostat which controlled the motor speed. It was in a very poor condition, rusty and all electrical parts visibly corroded and the original fabric insulation on the wiring had rotten. I was given this machine to repair & restore – a National Electric watch cleaning machine Model 1 which dates from the 1940’s.
